The Manufacturing Skills Gap: Current State and Future Outlook
Executive Summary The United States manufacturing sector is experiencing a persistent "skills gap" – a shortage of qualified workers for open skilled trade positions – even as the industry expands. Coming out of the pandemic, manufacturing employment has rebounded above 12.7 million (slightly higher than pre-2020 levels). Yet companies across all manufacturing sectors report difficulty finding talent, from entry-level operators to experienced technicians. This labor shortfall is not only an HR problem but an economic one: one study estimated that 2.1 million manufacturing jobs could go unfilled by 2030, potentially costing the U.S. economy $1 trillion in lost output that year alone. This report examines the current state of this skills gap in 2025, including demand vs. supply imbalances, regional and occupational impacts, and education pipeline trends, and explores how industry initiatives and new technologies are being leveraged to close the gap. Table of Contents 2025: Current State of the Manufacturing Skills Gap Regional and Sector Impacts Occupations Most Impacted Talent Pipeline: Trade School and Community College Trends Attracting New Talent: Which Trades Are Easier or Harder to Fill? Industry Initiatives and Technology Strategies to Bridge the Gap Outlook to 2035: Projections and Future Scenarios 2025: Current State of the Manufacturing Skills Gap As of early 2025, U.S. manufacturing faces a significant mismatch between labor supply and demand. Job openings in manufacturing remain elevated, even after some post-pandemic cooling. For instance, there were 622,000 unfilled manufacturing jobs nationally in January 2024, and about 462,000 openings still in January 2025. This means hundreds of thousands of factory positions are going unfilled at any given time. By mid-2024 there were signs of temporary relief – July 2024 was the first month since 2021 where the number of unemployed manufacturing workers slightly exceeded the number of job vacancies – but overall the labor market remains extremely tight. Nationwide, the ratio of unemployed persons to job openings has hovered around 0.9 (i.e. fewer than one available worker per opening) in recent months, and mid-decade demographic trends (low population growth and labor participation, plus retirements) suggest labor shortages will persist. Regional and Sector Impacts The skills gap is widespread across the country, though some regions feel it more acutely. Virtually every state has more manufacturing jobs open than workers to fill them. In states with robust manufacturing growth and very low unemployment, the imbalance is extreme. For example: New Hampshire had only 28 available workers for every 100 manufacturing job openings as of late 2023 Nebraska had just 39 per 100 openings North Carolina about 55 per 100 openings Even large states like Texas and Michigan report chronic shortages of skilled tradespeople in their manufacturing hubs. Generally, the Midwest and South – heartlands of automotive, aerospace, and heavy industry – report difficulty replacing an aging skilled workforce. At the same time, fast-growing manufacturing states in the Mountain West and Southeast (with many new factories breaking ground) are scrambling to attract enough trade workers to staff those operations. The breadth of the shortage is notable: it spans all major manufacturing sectors (from metal fabrication to food processing) and affects both durable goods and nondurable goods producers. Even after accounting for a recent dip in demand for manufactured goods in late 2024, manufacturers still cannot find enough qualified employees in many locales. Occupations Most Impacted A range of skilled trade and production roles are in short supply. Notably, skilled maintenance technicians, welders, machinists, and industrial electricians are among the hardest positions to fill, according to industry surveys. For example, the United States faces an acute welding shortage – the average welder is nearing retirement age, and the American Welding Society estimates a gap of over 400,000 welders by the mid-2020s. This shortage is starkly illustrated by demographics: for every five welders retiring or leaving the trade, only about one new person is entering it. Similarly, employers report difficulty finding CNC machinists and tool-and-die makers, critical roles for precision manufacturing. Many veteran machinists are retiring after decades on the job, and too few younger workers are replacing them – the current shortage of CNC machine operators is roughly three times worse than it was a decade ago. Industrial maintenance mechanics (who keep complex factory equipment running) are also in high demand as plants become more automated; these roles require both mechanical know-how and digital skills, a combination that is relatively scarce. In addition, licensed electricians (needed for both facility maintenance and equipment inst
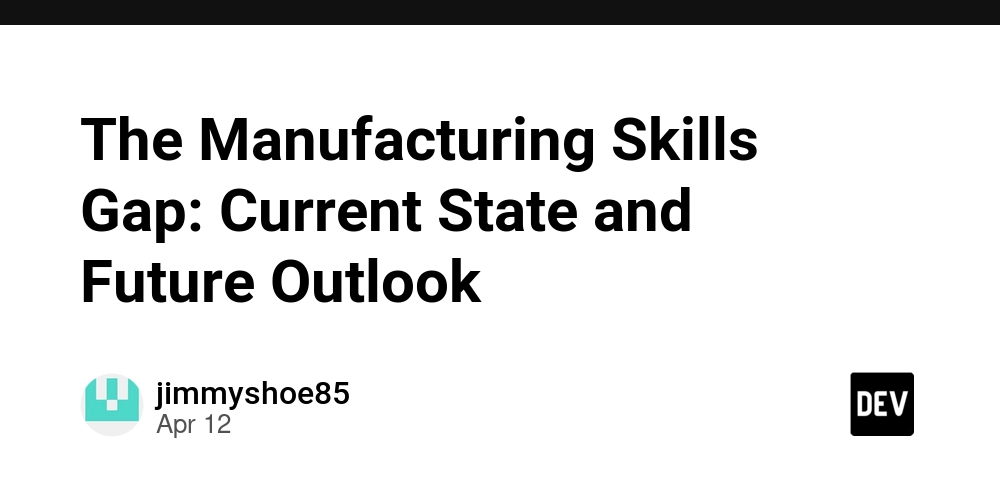
Executive Summary
The United States manufacturing sector is experiencing a persistent "skills gap" – a shortage of qualified workers for open skilled trade positions – even as the industry expands. Coming out of the pandemic, manufacturing employment has rebounded above 12.7 million (slightly higher than pre-2020 levels). Yet companies across all manufacturing sectors report difficulty finding talent, from entry-level operators to experienced technicians.
This labor shortfall is not only an HR problem but an economic one: one study estimated that 2.1 million manufacturing jobs could go unfilled by 2030, potentially costing the U.S. economy $1 trillion in lost output that year alone. This report examines the current state of this skills gap in 2025, including demand vs. supply imbalances, regional and occupational impacts, and education pipeline trends, and explores how industry initiatives and new technologies are being leveraged to close the gap.
Table of Contents
- 2025: Current State of the Manufacturing Skills Gap
- Regional and Sector Impacts
- Occupations Most Impacted
- Talent Pipeline: Trade School and Community College Trends
- Attracting New Talent: Which Trades Are Easier or Harder to Fill?
- Industry Initiatives and Technology Strategies to Bridge the Gap
- Outlook to 2035: Projections and Future Scenarios
2025: Current State of the Manufacturing Skills Gap
As of early 2025, U.S. manufacturing faces a significant mismatch between labor supply and demand. Job openings in manufacturing remain elevated, even after some post-pandemic cooling. For instance, there were 622,000 unfilled manufacturing jobs nationally in January 2024, and about 462,000 openings still in January 2025.
This means hundreds of thousands of factory positions are going unfilled at any given time. By mid-2024 there were signs of temporary relief – July 2024 was the first month since 2021 where the number of unemployed manufacturing workers slightly exceeded the number of job vacancies – but overall the labor market remains extremely tight.
Nationwide, the ratio of unemployed persons to job openings has hovered around 0.9 (i.e. fewer than one available worker per opening) in recent months, and mid-decade demographic trends (low population growth and labor participation, plus retirements) suggest labor shortages will persist.
Regional and Sector Impacts
The skills gap is widespread across the country, though some regions feel it more acutely. Virtually every state has more manufacturing jobs open than workers to fill them. In states with robust manufacturing growth and very low unemployment, the imbalance is extreme. For example:
- New Hampshire had only 28 available workers for every 100 manufacturing job openings as of late 2023
- Nebraska had just 39 per 100 openings
- North Carolina about 55 per 100 openings
Even large states like Texas and Michigan report chronic shortages of skilled tradespeople in their manufacturing hubs. Generally, the Midwest and South – heartlands of automotive, aerospace, and heavy industry – report difficulty replacing an aging skilled workforce. At the same time, fast-growing manufacturing states in the Mountain West and Southeast (with many new factories breaking ground) are scrambling to attract enough trade workers to staff those operations.
The breadth of the shortage is notable: it spans all major manufacturing sectors (from metal fabrication to food processing) and affects both durable goods and nondurable goods producers. Even after accounting for a recent dip in demand for manufactured goods in late 2024, manufacturers still cannot find enough qualified employees in many locales.
Occupations Most Impacted
A range of skilled trade and production roles are in short supply. Notably, skilled maintenance technicians, welders, machinists, and industrial electricians are among the hardest positions to fill, according to industry surveys.
For example, the United States faces an acute welding shortage – the average welder is nearing retirement age, and the American Welding Society estimates a gap of over 400,000 welders by the mid-2020s. This shortage is starkly illustrated by demographics: for every five welders retiring or leaving the trade, only about one new person is entering it.
Similarly, employers report difficulty finding CNC machinists and tool-and-die makers, critical roles for precision manufacturing. Many veteran machinists are retiring after decades on the job, and too few younger workers are replacing them – the current shortage of CNC machine operators is roughly three times worse than it was a decade ago.
Industrial maintenance mechanics (who keep complex factory equipment running) are also in high demand as plants become more automated; these roles require both mechanical know-how and digital skills, a combination that is relatively scarce. In addition, licensed electricians (needed for both facility maintenance and equipment installation) rank among the top ten hardest-to-fill occupations nationwide.
Even entry-level production operators and assemblers are hard to hire in some regions. The challenge cuts across skill levels: companies need more workers in every category, "from entry-level associates to skilled production workers to engineers." In short, the entire manufacturing talent pipeline is under strain, with certain skilled trades reaching crisis levels of unfilled positions.
Talent Pipeline: Trade School and Community College Trends
A major factor in the skills gap is the pipeline of new skilled workers entering trades via education and training programs. Over the past decade, traditional training pathways for manufacturing trades have not kept pace with industry needs. Graduation data shows that while the number of bachelor's degrees in the U.S. grew significantly from 2011 to 2022, the number of associate degrees (two-year programs often tied to technical and industrial skills) was essentially flat.
In other words, the output of community colleges in high-skill trades has stagnated. This is concerning because associate programs in fields like advanced manufacturing technology, welding technology, or engineering technology are key to producing technicians and mid-level skilled workers.
Encouragingly, the tide may be starting to turn post-pandemic. After years of declining interest, enrollment in vocational and trade programs is rebounding. Fall 2023 saw a 16% jump in the number of students enrolled in vocational-focused programs at community colleges – reaching the highest level since tracking began in 2018. Overall, trade school enrollment grew ~4.9% from 2020 to 2023, reversing pre-2020 declines. During the same period, traditional university enrollment fell about 0.6%.
However, not all skilled trade disciplines are benefitting equally from this renewed interest. Enrollment data shows that some trades programs have become much more popular than others:
Education Pathway | Enrollment Trend (Post-2020) |
---|---|
Trade/vocational programs (overall) | +4.9% (2020–2023 growth) |
Vocational programs @ community colleges | +16% (increase in 2023 vs. 2022) |
Construction trade programs | +23% (2023 vs. 2022) |
HVAC & auto maintenance programs | +7% (2023 vs. 2022) |
University (4-year college) enrollment | –0.6% (2020–2023 decline) |
These trends show a promising uptick in interest for trades, but from a relatively low base. Prior to 2020, many skilled trade schools saw annual enrollment declines around 4%. Now there is growth, but even a few percentage points per year may not be enough to compensate for the wave of retirements hitting manufacturing.
It's also notable that a few specialized sectors dominate trade education enrollment – for example, cosmetology (beauty and wellness) and healthcare technician programs together account for hundreds of thousands of students, whereas programs explicitly focused on manufacturing skills (like welding, machining, or mechatronics) have far fewer students.
The bottom line: interest in skilled trades careers is rising, but the training pipeline is still not producing talent at the volume needed to meet 100% of manufacturing labor demand.
Attracting New Talent: Which Trades Are Easier or Harder to Fill?
Not all skilled trades positions face the same level of recruitment challenge. Some trades are benefiting from improved perceptions and strong wage growth, making it a bit easier to entice new talent, while others continue to struggle with an image or awareness problem.
Welders
Despite high demand and decent pay, welding remains a hard-to-fill trade. The work can be physically demanding (involving heat, heavy equipment, and sometimes odd hours), and historically it has not been promoted to students as a desirable career. As a result, the average U.S. welder is in their mid-50s, and retirements are outpacing new entrants by a 5-to-1 ratio. This makes welding one of the most acute shortages.
Industrial Maintenance & Mechatronics
This field – which includes maintaining and repairing factory machinery, robotics, and automated systems – is crucial in advanced manufacturing. It requires a blend of mechanical skill and computer/electrical know-how. Many manufacturers report maintenance techs are very difficult to hire, as the role traditionally was learned through years of on-the-job training and apprenticeships, which have declined.
One advantage is that these roles are increasingly high-tech and problem-solving oriented, which can appeal to younger workers who enjoy technology. Some companies have had success attracting talent by rebranding maintenance roles as "industrial automation technician" or "mechatronics specialist," highlighting the tech aspect.
Electricians and Plumbers
Skilled trades like electrical work and plumbing (often categorized under construction trades but also critical for manufacturing facilities) have generally seen strong interest from new workers relative to other trades. These occupations are well-known, offer clear apprenticeship/journeyman paths, and enjoy a reputation for good pay and job security.
Despite this popularity, there is still a shortage – the construction and manufacturing boom means demand outstrips supply of licensed electricians, and a wave of retirements looms here too.
Machinists and Tool-and-Die Makers
These precision manufacturing roles are among the hardest to fill, largely due to a lack of visibility. Many young people simply don't know what a machinist or toolmaker does – these jobs aren't often mentioned in high school career counseling. Moreover, they carry the outdated stigma of being "dirty factory jobs," which in reality is an increasingly inaccurate picture (modern machining centers are often clean, high-tech environments).
"New collar" tech roles
On a positive note, manufacturers have found it easier to attract talent into some emerging roles that combine tech with hands-on work. For example, positions like robotics technician, 3D printing specialist, or CNC programmer often appeal to younger workers who have grown up with computers and electronics. These roles are often seen as cool, cutting-edge jobs in advanced manufacturing.
Industry Initiatives and Technology Strategies to Bridge the Gap
To combat the skills gap, manufacturers, educators, and policymakers are deploying a range of initiatives. Broadly, strategies fall into two categories: workforce development programs (to grow and upskill the human talent pipeline) and technology solutions (to mitigate the gap by increasing productivity or automating certain tasks).
Enhancing Workforce Development and Training
Apprenticeships and Earn-and-Learn Programs: Many companies have revived apprenticeship programs to train the next generation of skilled trades workers. These programs, often in partnership with unions or community colleges, allow trainees to earn a wage while learning on the job under mentorship.
A notable example is the FAME program (Federation for Advanced Manufacturing Education), originally founded by Toyota and now spread to dozens of manufacturers via the Manufacturing Institute. FAME is a 2-year earn-and-learn model producing multi-skilled technicians, and it has expanded to 40+ chapters in 16 states.
Partnerships with Schools and Community Colleges: Companies are increasingly collaborating with local educational institutions to align curricula with industry needs. This "talent ecosystem" approach involves manufacturers providing equipment, guest instructors, or internship opportunities to high schools, trade schools, and community colleges.
Upskilling Current Workers: Retaining and retraining existing employees is another crucial tactic. Given the difficulty in hiring externally, manufacturers are focusing on upskilling their incumbent workforce – teaching new skills to current employees so they can fill more advanced roles.
According to a 2024 industry survey, 56% of manufacturers said they are providing internal upskilling to help address talent shortages. Many large firms have established in-house training academies or "universities."
Improving Perception and Outreach: Changing the image of manufacturing careers is a long-term strategy. Industry associations and companies sponsor outreach initiatives such as Manufacturing Day (plant tours and demos each October), social media campaigns highlighting young people in trades, and engagement with K-12 schools (like robotics competitions or skilled trades summer camps).
There is also a push to diversify the talent pool: recruiting more women, minorities, and veterans into manufacturing. Programs like Women in Manufacturing and Heroes MAKE America (for transitioning military veterans) are helping broaden the workforce.
Embracing Automation, AI, and Advanced Technology
Industrial Automation & Robotics: Automating repetitive or labor-intensive tasks can alleviate the need for as many manual workers. Many manufacturers are accelerating investments in robotics – from robotic welders in fabrication shops to autonomous guided vehicles (AGVs) for material handling in warehouses.
For example, faced with the welder shortage, some companies have deployed robotic welding cells that one operator can oversee, effectively doing the work of multiple welders. Similarly, machine shops are adding robotic machine tending systems to run CNC machines lights-out (overnight with minimal human intervention).
Advanced Analytics and AI for Workforce Management: Manufacturers are also using software to optimize how they utilize the talent they do have. Workforce management systems help with smarter scheduling, demand forecasting, and skill tracking.
By digitizing skills matrices and employee certifications, companies can quickly identify internal skill gaps and coordinate training or hiring to fill them. Some are using AI-based scheduling that can accommodate workers' preferences (improving work-life balance) while ensuring shifts are covered efficiently.
AI, Simulation, and XR for Training: Another technology approach addresses the skills gap by speeding up how quickly new or existing employees can be trained. Manufacturers are exploring extended reality (XR) – including virtual reality and augmented reality – to enhance training programs.
For example, VR training modules can simulate a welding environment or a machine repair task in a safe, controlled virtual space, allowing trainees to practice and build skills faster. Augmented reality can overlay step-by-step instructions or diagrams onto a technician's field of view when servicing complex equipment, effectively lowering the skill threshold needed for certain tasks.
Process Improvement and Intelligent Operations: Beyond direct automation of labor, manufacturers are adopting Industry 4.0 technologies (IoT sensors, data analytics, predictive maintenance, etc.) to improve productivity and reduce reliance on brute-force labor.
For instance, predictive maintenance systems can foresee equipment failures and schedule repairs proactively, meaning maintenance teams (which are understaffed) can work more efficiently and avoid catastrophic breakdowns that would require all hands on deck.
Outlook to 2035: Projections and Future Scenarios
Looking ahead to 2035, will the manufacturing skills gap narrow, or will it persist (or even widen)? Based on current trends and projections, experts anticipate that the challenge will remain significant over the next decade, though its nature may evolve.
Size of the Gap
If no major changes occur in the talent pipeline, the gap could stay extremely large. Deloitte and The Manufacturing Institute's latest talent study (2024) forecasts that the U.S. manufacturing industry will need to hire about 3.8 million workers between 2024 and 2033 to support growth and replace retirees. Of those, approximately 1.9 million jobs could remain unfilled if the industry doesn't solve the skills and applicant gaps.
That implies roughly half of the openings might go unstaffed. Extrapolating to 2035, and considering the trajectory of baby boomer retirements, it's plausible that on the order of 2+ million positions in manufacturing might be unfilled a decade from now.
Continued Retirement Wave
The demographic headwinds will intensify through the 2020s. Nearly one-third of the manufacturing workforce is 55+ today. By 2035, those individuals will be 65-75 years old – most will have retired. That represents millions of skilled tradespeople exiting.
For perspective, Deloitte's analysis attributed 2.8 million of the 2024–2033 job openings to retirements alone. We can expect a similar magnitude of retirements in the early 2030s. This will especially hit skilled trades that skew older (e.g. many tool & die makers, master welders, senior maintenance techs).
Impact of Technology by 2035
The next decade will likely see accelerated automation in manufacturing, partly out of necessity. By 2035, we can expect that many rote and physically intensive tasks in factories will be largely automated or assisted by machines. This could alleviate shortages in some entry-level roles.
However, new skills gaps may emerge. The demand for human labor will shift toward overseeing and maintaining automated systems, programming machines, and other higher-skilled roles. This could create a gap in high-tech skills – e.g. not enough robotics technicians or data analysts for smart factories – if training doesn't keep up.
We might also see more AI-driven worker augmentation: by 2035, AI copilots could be common on the shop floor (for instance, an AI assistant that a technician can consult for repair guidance). This would lower skill barriers for certain jobs, potentially allowing less-experienced workers to perform tasks that used to require 20-year veterans.
Education and Pipeline in 10 Years
The recent uptick in trade school enrollment is an encouraging sign for 2035. If that momentum continues, the pipeline of new tradespeople should improve. Let's say trade/vocational program enrollment grows 5-7% annually – by 2030, that could produce a significantly larger graduating class of welders, machinists, etc.
There is also a broader trend toward "skills-based hiring" in the economy, which might benefit trades. More emphasis on apprenticeships, certificates, and on-the-job skills (versus degrees) could channel more people into vocational paths.
Overall, most analysts believe the manufacturing talent pipeline will improve incrementally, but not explosively, by 2035. Thus there will likely still be a shortfall, albeit maybe a somewhat reduced one if enrollment and training trends stay positive.
Conclusion
As we approach 2035, the manufacturing skills gap is expected to persist as a critical challenge. Current forecasts suggest that, absent major changes, millions of manufacturing jobs will remain unfilled over the next decade.
The gap will be driven largely by retirements outpacing new entrants, alongside the creation of new roles from industry growth and reshoring efforts. Automation and AI will help mitigate the shortfall but will also shift the skills needed from hands-on trades to more tech-centric roles.
The hope is that the many initiatives now in motion – from revitalizing trade education, to apprenticeship expansions, to aggressive technology adoption – will bear fruit over the coming decade. If they do, the gap in 2035 could be smaller in proportion than it is in 2025, allowing U.S. manufacturing to sustain its growth.
If they don't, the industry could be constrained by labor shortages, potentially missing out on productive capacity and economic gains (recall the projected $1 trillion cost of the gap by 2030 if unaddressed). In the years leading up to 2035, we can expect to see even more creative solutions aimed at finally closing the skills gap and securing the future of American manufacturing.