6 Key Factors Affecting Abrasive Blasting Results: An Optimization Guide for Engineers & Procurement Managers
Abrasive blasting is a widely used surface treatment technology in manufacturing, directly impacting coating adhesion, material durability, and product aesthetics. However, the success of blasting processes hinges on precise control of multiple variables. This article analyzes the 6 core factors influencing blasting outcomes from an industrial perspective, offering engineers actionable optimization strategies and equipping procurement managers with critical equipment selection insights. 1. Abrasive Media: The DNA of Surface Roughness Hardness & Shape: Aluminum oxide (Al₂O₃) for rust removal, glass beads for precision deburring, and steel grit for heavy-duty anti-corrosion treatment. Angular abrasives increase Ra values (surface roughness), while spherical media excel at surface polishing. Grit Size Selection: #40-#80 mesh (coarse) for thick oxide layers, #100-#220 (fine) for precision cleaning. Field data from an auto parts plant shows 80-mesh steel grit improves efficiency by 37% over 120-mesh but reduces coating adhesion by 15%. Cost Efficiency: Prioritize recyclability—brown fused alumina (85% reuse rate) offers lower long-term costs than disposable quartz sand. 2. Blasting Pressure: Precision Control of Kinetic Energy Pressure-Efficiency Curve: Cleaning efficiency grows linearly within 0.4-0.7 MPa but plummets above 0.8 MPa due to abrasive fragmentation. PID-controlled compressors reduce energy consumption by 18%. Material Sensitivity: Aluminum alloys require ≤0.5 MPa; cast iron tolerates 0.6-0.7 MPa. An aerospace manufacturer reduced thin-wall part deformation from 3.2% to 0.7% via pressure staging. 3. Nozzle Performance: The Overlooked Flow Amplifier Venturi Effect Utilization: Long-neck tungsten carbide nozzles boost airflow velocity by 40% vs. standard cylindrical designs. A shipyard increased daily coverage from 120㎡ to 170㎡ post-upgrade. Wear Monitoring: Replace nozzles when orifice expansion exceeds 10%—delayed replacement increases air consumption by 25%. Ceramic-lined nozzles triple lifespan. 4. Blasting Angle & Distance: Geometric Precision Matters Optimal Impact Angle: 75-90° vertical strikes maximize cleaning force; angles below 30° cause "plowing effects." Automated gun oscillation systems improve coverage from 68% to 94%. Distance Formula: D=15×d (d=nozzle diameter). A wind tower manufacturer reduced rework from 12% to 3.5% using laser distance control. 5. Substrate Properties: The Inherent Variable Hardness Matching: Abrasive hardness must exceed substrate by ≥1.5x. For H62 brass (HV120), garnet (HV180) outperforms glass beads by 40% in efficiency. Pre-treatment: Alkaline degreasing is mandatory for surfaces with >5g/㎡ oil content. An OEM reduced coating delamination complaints by 82% after implementing in-line oil detection. 6. Environmental Control: The Silent Quality Killer Humidity Risks: At >85% RH, every 1% increase in abrasive moisture raises salt contamination risk by 18%. Use dew point-monitored dry air systems. Dust Management: Cyclone + cartridge filter systems boost media reuse from 55% to 88% while meeting OSHA’s 15mg/m³ standard. FAQ Q1: When should abrasive media be replaced? A: Refresh media when >30% particles round or fracture. Use sieving machines for particle analysis. Q2: Why choose automated over manual blasting? A: Robotic systems (e.g., 6-axis wheel hub lines) improve consistency from ±15% to ±5% and cut labor costs by 60%. Q3: How to blast complex cavities? A: 3D vortex nozzles with spiral airflow increase internal coverage from 55% to 90%. Mastering these six factors enhances process repeatability and cost efficiency. Engineers should build parameter matrices, while procurement teams should prioritize IoT-enabled blasting systems. Optimized processes reduce coating costs by 22% and extend product lifespan by 40% (SGS lab data).
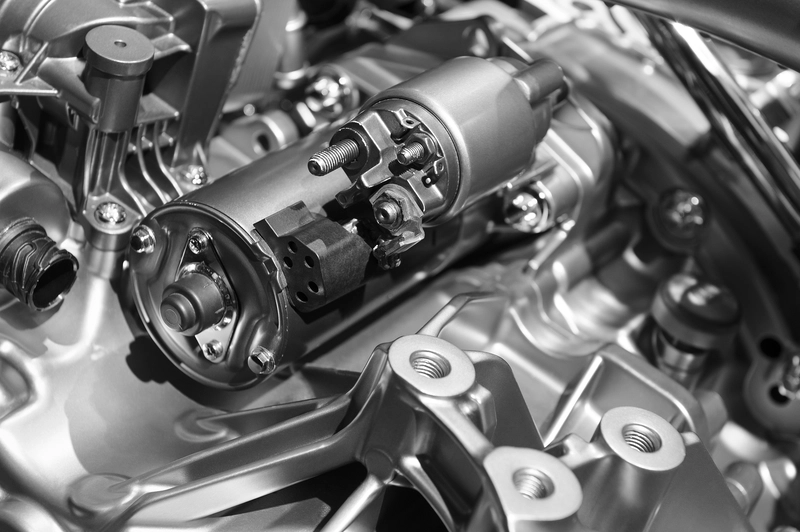
Abrasive blasting is a widely used surface treatment technology in manufacturing, directly impacting coating adhesion, material durability, and product aesthetics. However, the success of blasting processes hinges on precise control of multiple variables. This article analyzes the 6 core factors influencing blasting outcomes from an industrial perspective, offering engineers actionable optimization strategies and equipping procurement managers with critical equipment selection insights.
1. Abrasive Media: The DNA of Surface Roughness
- Hardness & Shape: Aluminum oxide (Al₂O₃) for rust removal, glass beads for precision deburring, and steel grit for heavy-duty anti-corrosion treatment. Angular abrasives increase Ra values (surface roughness), while spherical media excel at surface polishing.
- Grit Size Selection: #40-#80 mesh (coarse) for thick oxide layers, #100-#220 (fine) for precision cleaning. Field data from an auto parts plant shows 80-mesh steel grit improves efficiency by 37% over 120-mesh but reduces coating adhesion by 15%.
- Cost Efficiency: Prioritize recyclability—brown fused alumina (85% reuse rate) offers lower long-term costs than disposable quartz sand.
2. Blasting Pressure: Precision Control of Kinetic Energy
- Pressure-Efficiency Curve: Cleaning efficiency grows linearly within 0.4-0.7 MPa but plummets above 0.8 MPa due to abrasive fragmentation. PID-controlled compressors reduce energy consumption by 18%.
- Material Sensitivity: Aluminum alloys require ≤0.5 MPa; cast iron tolerates 0.6-0.7 MPa. An aerospace manufacturer reduced thin-wall part deformation from 3.2% to 0.7% via pressure staging.
3. Nozzle Performance: The Overlooked Flow Amplifier
- Venturi Effect Utilization: Long-neck tungsten carbide nozzles boost airflow velocity by 40% vs. standard cylindrical designs. A shipyard increased daily coverage from 120㎡ to 170㎡ post-upgrade.
- Wear Monitoring: Replace nozzles when orifice expansion exceeds 10%—delayed replacement increases air consumption by 25%. Ceramic-lined nozzles triple lifespan.
4. Blasting Angle & Distance: Geometric Precision Matters
- Optimal Impact Angle: 75-90° vertical strikes maximize cleaning force; angles below 30° cause "plowing effects." Automated gun oscillation systems improve coverage from 68% to 94%.
- Distance Formula: D=15×d (d=nozzle diameter). A wind tower manufacturer reduced rework from 12% to 3.5% using laser distance control.
5. Substrate Properties: The Inherent Variable
- Hardness Matching: Abrasive hardness must exceed substrate by ≥1.5x. For H62 brass (HV120), garnet (HV180) outperforms glass beads by 40% in efficiency.
- Pre-treatment: Alkaline degreasing is mandatory for surfaces with >5g/㎡ oil content. An OEM reduced coating delamination complaints by 82% after implementing in-line oil detection.
6. Environmental Control: The Silent Quality Killer
- Humidity Risks: At >85% RH, every 1% increase in abrasive moisture raises salt contamination risk by 18%. Use dew point-monitored dry air systems.
- Dust Management: Cyclone + cartridge filter systems boost media reuse from 55% to 88% while meeting OSHA’s 15mg/m³ standard.
FAQ
Q1: When should abrasive media be replaced?
A: Refresh media when >30% particles round or fracture. Use sieving machines for particle analysis.
Q2: Why choose automated over manual blasting?
A: Robotic systems (e.g., 6-axis wheel hub lines) improve consistency from ±15% to ±5% and cut labor costs by 60%.
Q3: How to blast complex cavities?
A: 3D vortex nozzles with spiral airflow increase internal coverage from 55% to 90%.
Mastering these six factors enhances process repeatability and cost efficiency. Engineers should build parameter matrices, while procurement teams should prioritize IoT-enabled blasting systems. Optimized processes reduce coating costs by 22% and extend product lifespan by 40% (SGS lab data).